Fracture Fix
A student team’s magnetic design simplifies the surgical repair of broken bones.
Last academic year, Rice seniors in the Brown School of Engineering set out to help doctors simplify the process of repairing fractured long bones in an arm or leg by inventing a mechanism that uses magnets to set things right. Their project took first place in the 2019 Engineering Design Showcase competition.
The students, who called themselves Drill Team Six, chose the project pitched by Ashvin Dewan ’05, an orthopedic surgeon at Houston Methodist Hospital. The goal was to simplify a procedure by which titanium rods are placed inside broken bones to make them functional once more.
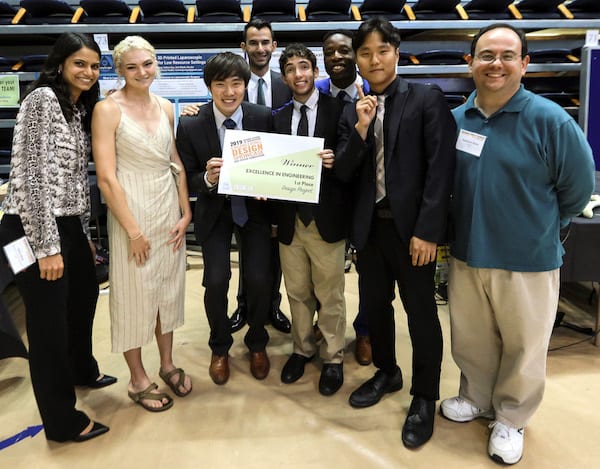
The team — bioengineering majors Babs Ogunbanwo, Takanori Iida, Byunguk Kang and Hannah Jackson and mechanical engineering majors Will Yarinsky and Ian Frankel — learned from Dewan that surgeons require many X-rays to locate predrilled 5 millimeter holes in the rod. The holes allow them to secure the rod to the bone fragments and hold them together.
Drill Team Six, from left, adviser and bioengineering lecturer Sabia Abidi, Hannah Jackson, Takanori Iida, Will Yarinsky, Ian Frankel, Babs Ogunbanwo, Byung-UK Kang and Matthew Elliott, a lecturer in mechanical engineering. Photo by An Le/Luxe Studio Productions
The surgery typically requires doctors to insert the long rod with a guide wire into the end of the bone, drilling through marrow to align the fragments. With that done, they depend on X-rays, their experience and, if necessary, a bit of trial and error to drill long surgical screws through one side of the bone, thread it through the rod and secure it to the other side.
The Rice team would make the wire adjacent to the holes magnetic, because neither skin nor bone hinder a magnetic field. “That way, the magnets hold their position and we can do the location process,” Frankel said. “Once we’ve found them and secured the rod, we remove the wire and the magnets with it.”
The exterior mechanism is a brace that can be securely attached to the arm or leg with Velcro. A mounted sensor can then be moved along the 3D-printed carbon-fiber rods or around the limb until it locates the magnet. The angle of the sensor can be adjusted. As each of the three degrees of freedom come into alignment with the target, a “virtual LED” lights up on a graphic display wired to the sensor. Then, the sensor is removed and a drill keyed to the mechanism inserted.
Working at Rice’s Oshman Engineering Design Kitchen, the team tested its device on a mannequin leg and a “wooden leg,” a frame that allowed for mounting the rod with its magnetized wire and checking the accuracy of their system. Results are promising, but there’s much more development ahead before the device can be used by clinicians.
A new team of Rice engineering students has taken over the project for the 2019–2020 academic year. Watch for more news about this invention from Team Sensorautomation.